HYLMAN puts forth techniques, processes, and methodologies to ensure the clients are receiving the right level of support beyond the flaws of man, technology or the environment.
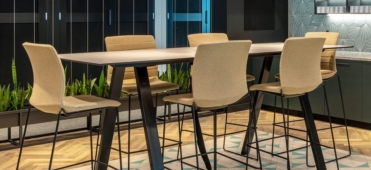
HYLMAN puts forth techniques, processes, and methodologies to ensure the clients are receiving the right level of support beyond the flaws of man, technology or the environment.
Besides having a 3-tiered support system of backup experts in support for every lead expert for both support and replacement in the case that unforeseen circumstances occur, such as the effect of the pandemic, fluctuations in work demand, or absenteeism, HYLMAN has a highly efficient working structure to meet all kinds of fluctuating demands and peaks of workload, throughout any project or workstream, during normal or abnormal times and during times of lead deployed teams’ potential absence or times of holidays. We strive to keep the best orientation and response time/mobilisation to all kinds of engagements, around the clock and even outside working hours.
This is done through operating under different schedules (Sun-Thu, Mon-Fri, and dedicated Sat oncalls, morning schedules/night schedules, and rotational orientation). The way consistency is approached is by maintaining the generic contact point that all response teams for deployment have access to as management and coordinators. According to stats, the team at HYLMAN have maintained a 90%+ response rate so far (which is an indicator of the time to response, quality of response, satisfaction of the recipient/client, feedback on support, and time to engagement). The time to respond to a specific contact point, if at anytime extra hands are needed or identified by the client, is usually within the hour at anytime during the working day, slightly higher outside normal working hours at 1-2 hours, unless the query requires partners/directors inputs in more complex scenarios in which case can take between 2-6 hours.
All queries for engagement or replacement thereof go through a ticketing and management tool that assesses complexity, urgency, and persons of concern to mobilise. Support staff often assess immediately and share the necessary info then respond to the query in a prompt fashion. The contact point is deployment@consultingcentrale.com, which is dedicated for deployment in any country that our applicable teams would support. Suffice it to say that any position or delivery would not be missed throughout any project’s lifetime.
HYLMAN’s service best practice includes continuous improvement processes from each delivery team as part of any delivery cycle to capture key learnings which may be of value to clients. Structured "Experiential Learning" workshops are held with the delivery team, steercos and relevant stakeholders that use a defined agenda from pre-held internal review and are run by managers who are not directly involved in the delivery. Customer feedback are often sought before the workshops as part of the closure interview through our official feedback procedure, or the customer is invited to the session to share their feedback or suggestions directly. Lessons learned may be reviewed at key milestones and at the end of assignments.
Our corporate, long term commitment to quality and continuous improvement Delivery methodology complies with BS-EN-ISO-9001 standards and incorporates a proven process and toolsets for measuring the quality of operational services and progress against their implementation plan covering participant satisfaction level, monitoring and progression of participants, and quantifiable and qualitative outputs as outlined for the delivery of the programmes. All quality management systems employed to monitor the quality of operational services and progress are subject to a rigorous and consistent process of quality control, risk registry to assess the levels of risk associated in terms of performance and delivery, and contingency plans for the high risk/substandard delivery according to the registered elements.
Experiential Learning materials are reviewed by the relevant Practice Continuous
Improvement Controller and Lead from HYLMAN, often the overarching director in a project or second tier in line. They assess the impact and relevance of the learning to ensure that actions are taken to make any necessary changes. Problems with operational processes are acted on by the Operations Manager. The Continuous Improvement Lead will approve the resulting plan, risk registry and contingencies on the knowledge tool and will inform colleagues from other commissions who could encounter similar issues so they can learn from the experience within the framework. Colleagues responsible for the maintenance and development of these tools will routinely scan it to learn from current experiences.
Key lessons are documented in a business continuity report that includes risk register and contingency plans, along with any comments for anticipating unplanned events that can hurdle progress. Reusable material such as service designs, reusable processes, checklists, example plans, methodologies from protocols and reports are included in the Experiential Learning pack so that the client and other teams can derive better value and reduced risk customisations or variation using lean six sigma best practices and by re-using the employed improvements proven by the other teams.
Leading complex journeys across different functions
Supporting deliveries internationally with the local feel
Bringing in the mix of knowledge, intellect and culture
Available to service clients around the clock and satisfy their needs
Provide added value with social responsibility, value for money,
intelligence, and systematic support